Products Description
Working principle:
The useful waste gas enters the regenerative chamber 1 through the induced draft fan to absorb heat, and then enters the incineration chamber for further heating after heating, so that the useful waste gas continues to heat up until the useful components are thoroughly decomposed into CO2 and H2O. Since the waste gas uses the heat recovered by the regenerative body during the heating process, the fuel consumption is relatively low. After being treated, the waste gas leaves the combustion chamber and enters the regenerative chamber 2 to release heat and then be discharged, while the regenerative body of the regenerative chamber 2 absorbs heat and is used to heat the newly input low-temperature waste gas in the next cycle.
At the same time, part of the purified gas is introduced to purge the regenerative chamber 3 in preparation for the next round of heat exchange. After the process is completed, the air inlet and outlet valves are switched, the gas enters the regenerative chamber 2, is discharged from the regenerative chamber 3, and is purged in the regenerative chamber 1; the next cycle is switched to enter the regenerative chamber 3, discharge from the regenerative chamber 1, and purge the regenerative chamber 2, and the alternating switching continues. In addition, in order to improve the utilization rate of thermal energy, a heat exchanger can be set after the RTO incinerator to enhance the utilization of waste heat.
During the operation of the three-chamber RTO, a single regenerator switches repeatedly between the three states of air intake, cleaning, and exhaust. After a cycle, VOCs always enter the regenerator that discharged the purified gas in the previous cycle, while the regenerator that originally entered the VOCs is cleaned with purified gas or air, and the remaining unreacted VOCs are sent back to the combustion chamber for oxidation, and then discharged from the flushed regenerator together with the purified gas.
This process is constantly cycled and alternated, so that the heat emission after waste gas treatment is effectively reduced, and the heat loss during the oxidation and heating of waste gas is saved, so that the waste gas maintains a high thermal efficiency (thermal efficiency of about 90%) during the high-temperature oxidation process. The equipment has good performance, simple operation, convenient maintenance, low operating costs, and VOCs purification efficiency is as good as 90%.
Structural description
RTO furnace body
The furnace body consists of two or more regenerators and a combustion chamber. The regenerator performs preheating, purging, and heat storage functions in turn. The shell is made of 6mm carbon steel plate (surface sandblasting), with reinforcing ribs on the outer surface, the shell is well sealed, and the outer surface is painted with heat-resistant paint.
RTO furnace body insulation
The furnace combustion chamber and the regenerator are insulated with refractory aluminum silicate fiber, which is heat-resistant to 1200℃, with a fleece weight of 192kg/m3 and a thickness of 250mm. There are two layers of internal insulation, including one layer of ceramic fiber felt and one layer of ceramic fiber module. A heat-resistant steel skeleton is set in the ceramic fiber module, which is fixed to the furnace shell with anchors, and the outer surface is coated with actual reports. The surface temperature of the furnace body is +25 degrees ambient temperature and not more than 60℃.
RTO ceramic regenerator
The ceramic regenerator adopts Lantech MLM technology. MLM filler is composed of multiple layers of toothed ceramic sheets. Its reliable structural design not only has the characteristics of large specific surface area, high heat capacity, fast heat transfer, low pressure drop, and anti-fouling and clogging of traditional honeycomb ceramics, but also has the advantages of strong heat storage and easy molding of traditional bulk ceramic fillers such as saddle rings.
RTO combustion system
Use industrial burners. The system includes a combustion controller, a flame detector, a high-pressure igniter and a corresponding valve combination. The high-temperature sensor in the furnace can feedback the furnace temperature information to control the heating capacity of the burner, thereby stabilizing the furnace temperature at around 750℃.
RTO wind direction switching valve
RTO wind direction switching valves all use direct push cover valves, which have good valve accuracy, small leakage (≤1%), long life (up to 1 million times), suitable opening and closing speed (1s), and excellent operation. The actuator uses a pneumatic actuator, including a solenoid valve and a cylinder. The compressed air pressure of the pneumatic actuator is 0.4~0.6MPa.
RTO control system
This system adopts PLC programmable control. The system is mainly composed of the regulating object (furnace temperature), detection element (temperature measuring instrument), regulator and actuator. The control cabinet is equipped with human-machine interface (HMI) equipment for on-site operation prompts, fault alarms, operating parameter display, control parameter setting and equipment control.
Product advantages
1. Good concentration of waste gas treatment to achieve self-heating combustion, low operating costs and reasonable cost performance.
2. Good purification efficiency, three-chamber RTO can reach 90%.
3. Ceramic heat storage body is used as heat recovery, preheating and heat storage are operated alternately, and the thermal efficiency is ≥90%.
4. The steel structure of the furnace body is reliable, the insulation layer is thick, the operating performance is good, and the stability is high.
5. PLC programmable automatic control, good degree of automation.
6. Waste heat utilization, high economic benefits; excess heat energy is recycled to drying room, oven, etc., and the heating of the drying room does not consume additional fuel or electricity.
Scope of application
Applicable to printing, coating, petrochemical, fine chemical, textile printing and dyeing, rubber, chemical raw materials, compound fertilizers, pharmaceutical chemicals, daily chemicals, synthetic materials and other industries.
Tags:
Technical parameter
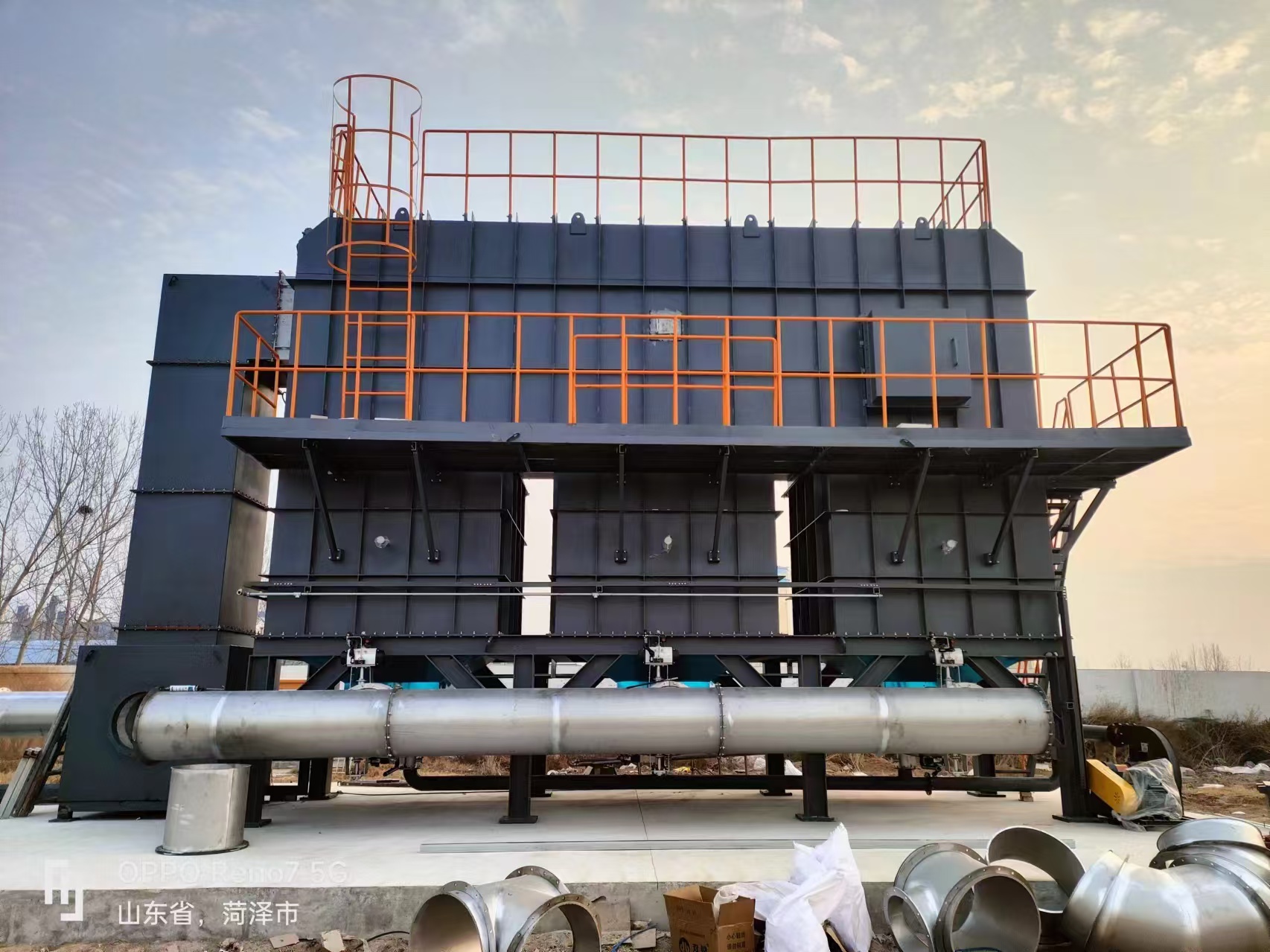
Three-chamber RTO regenerative thermal incinerator 1